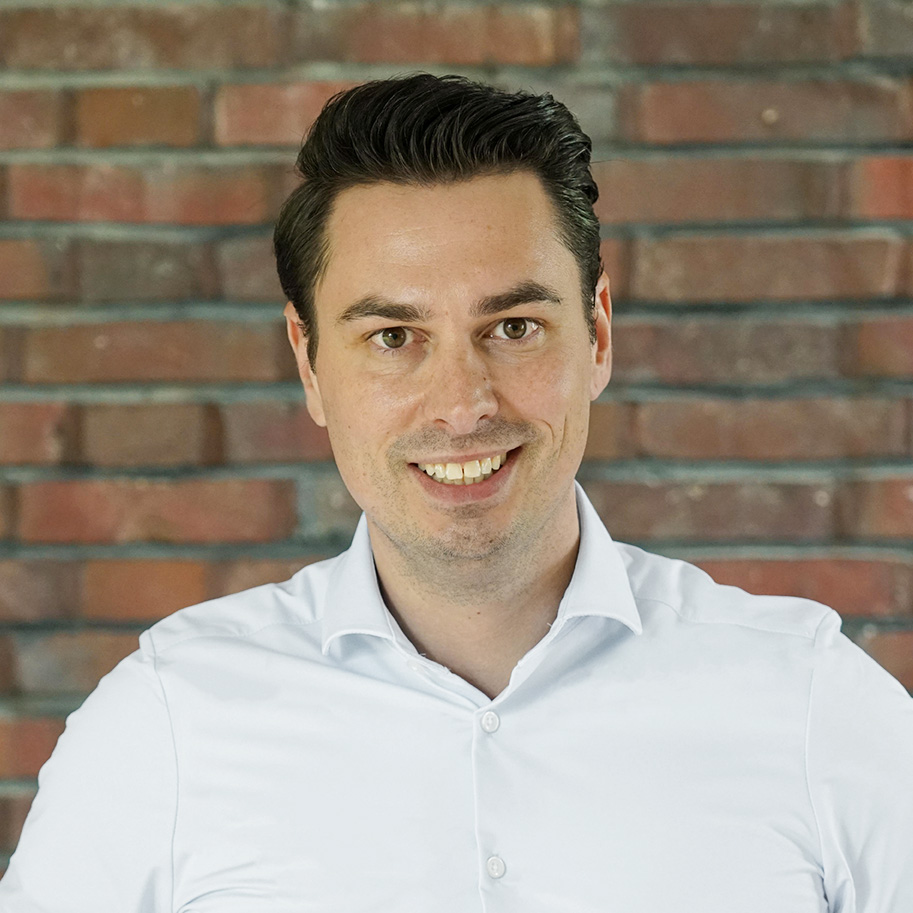
Das mittelständische Unternehmen FRANZ BALS GMBH aus Lippstadt ist spezialisiert auf die individuelle Fertigung von Federprodukten aus Bandstahl und Draht, welche in unterschiedlichen Branchen und Industrien weltweit eingesetzt werden. Dabei zeichnet sich das Unternehmen durch eine hohe Fertigungstiefe aus, welche eine flexible Produktion vom Prototypenbau bis Serienfertigung erlaubt.
In der Produktion kommen dabei neueste Generationen von CNC-Bearbeitungsmaschinen, Laserschneidanlagen und Zugfedervollautomaten zum Einsatz. Der moderne und leistungsstarke Maschinenpark wird um ENERGIEINTENSIVE PROZESSTECHNOLOGIEN zur Oberflächen- und Warmbehandlung sowie Baugruppenmontage u. a. mit diversen Schweißoperationen ergänzt.
Dazu wurde mit Hilfe der wfg.IOT-BOX über einen mehrwöchigen Zeitraum ein Energiemonitoring durchgeführt und die Daten auf einem Dashboard in der Produktion visualisiert. Das Ziel: Die Lastgangmessung sollen die notwendige Transparenz über den zeitlichen Verlauf von Prozesskenngrößen zur elektrischen Leistungsaufnahme bei einigen energieintensiven Prozesstechnologien liefern.
Bei vielen Industrieunternehmen ist neben der bezogenen Energie auch die höchste jährliche Lastspitze für die Berechnung der Stromkosten relevant. Die Netznutzungsentgelte (Leistungspreis) werden dabei anhand des maximalen mittleren Leistungsbezugs, meistens über einen 15 Minuten Intervall, berechnet. Demnach kann ein einzelner „Ausreißer“ im Berechnungszeitraum hohe Kosten verursachen.
Konkrete Lösungsansätze lieferte die datenbasierte Analyse mit der wfg.IOT-BOX. Dazu erfolgte ein digitales Retrofit an einer Widerstandschweißmaschine mit Steuerung des Herstellers BIHLER mit zugehörigem Kühlwasser Rückkühler des Herstellers HYFRA sowie zwei Industrieöfen der Hersteller NABERTHERM und THERMCONCEPT.
Als erster Ansatz wird nun die Verschiebung des Energiebezugs in Zeitbereiche geringer Gesamtleistung geprüft. Das zeitversetzte Hochfahren von Anlagen kann dabei durch einfache Arbeitsanweisungen schnell umgesetzt werden.
Ein weiterer Kostentreiber: Druckluft. Gemessen haben wir über den Projektzeitraum ebenfalls das Druckniveau und den Durchfluss.
Im Rahmen der Potentialanalyse mit der wfg.IOT-BOX konnten für die Franz Bals GmbH Einsparmöglichkeiten identifiziert und Optimierungsmaßnahmen in die Wege geleitet werden. Auch können die Daten zukünftig zur genaueren Berechnung eines CO2-Fußabdrucks von Bauteilen beitragen.
Melden Sie sich gerne bei uns. Hier finden Sie weitere Informationen
Dies ist ein kostenloses Angebot im Rahmen des Projektes „Produktion.Digital.Südwestfalen-PLUS“ und wird gefördert durch die Europäische Union und dem Ministerium für Wirtschaft, Industrie, Klimaschutz und Energie des Landes Nordrhein-Westfalen.